BoX Leg Console Table – Build Plans
This BoX Leg Console Table is a variation of my two-toned console table. This one with a large X in the box legs. The X’s are a fun addition and are easy to add when you use the technique used in my X leg bench. You could also ad an additional shelf in the middle like in my Three Shelf Console Table. There are so many different ways you can change up this one simple plan!
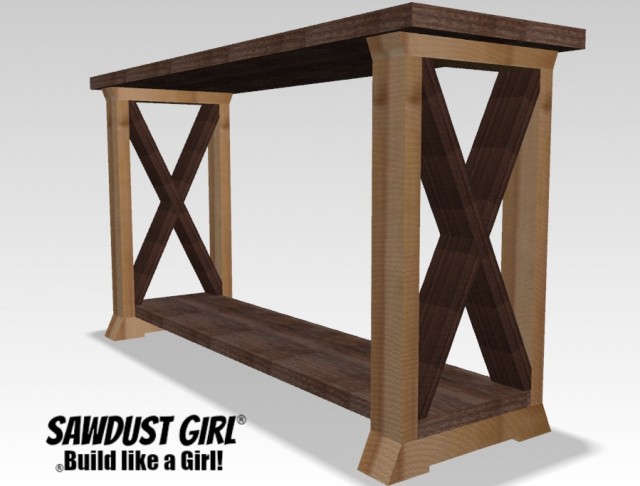
BoX Leg Console Table
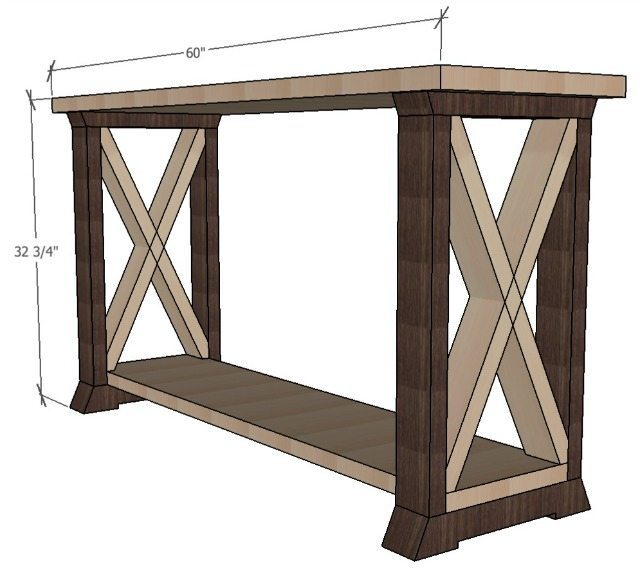
Materials
Lumber needed for table top and shelf:
- Join several pieces of 2x lumber to achieve desired width
(or greater than desired and then cut down to size) for table top and lower shelf. - Top is 18″ wide
- Lower shelf is 12″ (the leg opening is 12 7/16″ wide shelf should be less to allow for wood movement).
- In this drawing, the lower shelf ends with the legs but the top can overhang by a couple inches in each end. Of course you can modify the length of each to make your table fit your space.
2×4 Lumber lengths needed for legs:
- two – 16 5/8″
- four – 18″
- four – 27″
2×4 Lumber lengths for X’s:
- four – 29″
Basic Table Leg
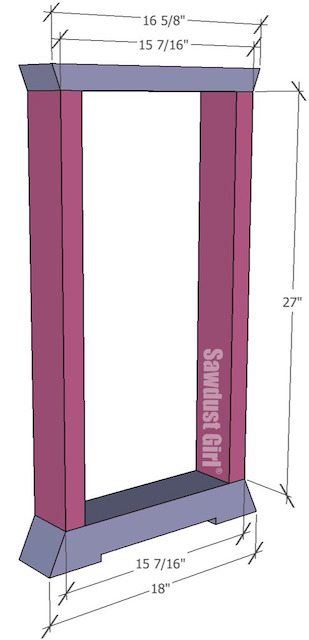
Step 1 – create leg bottom
- Use wood glue and clamps to join two 18″ long 2×4’s to create leg bottom.
- Create TWO 18″ long leg bottoms
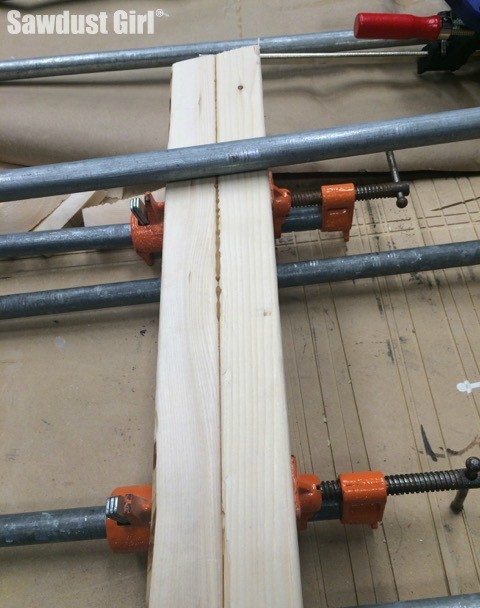
Optional Step
- If you have a jointer and thickness planer, joint and plane all your leg pieces to the same thickness at this point. The jointer makes quick work of that glue squeeze out.
- If you don’t have these tools, scrape away and sand off all traces of glue that squeeze out during clamping. Glue will not take stain and can really throw a wrench in your painstaking finish efforts.
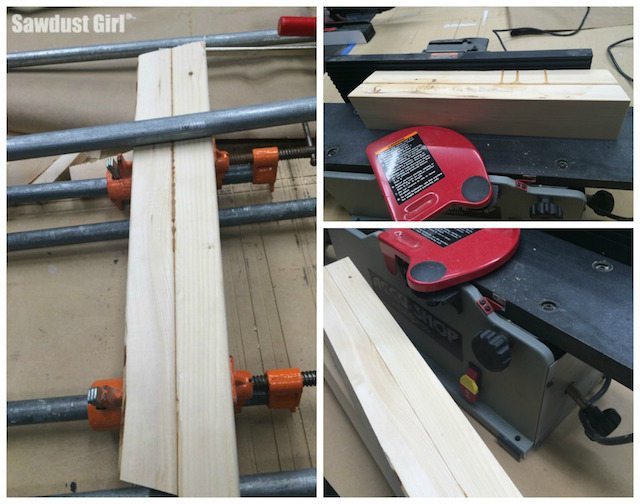
- Cut the ends of the leg tops (16 5/8″ long 2×4’s) and leg bottoms that you just created at a 15˚ angle.
- You can do this on a miter saw or table saw or with a straight edge guide and a circular saw.
- If you do not cut 15˚ angles, trim the leg bottoms to the same length as the top.
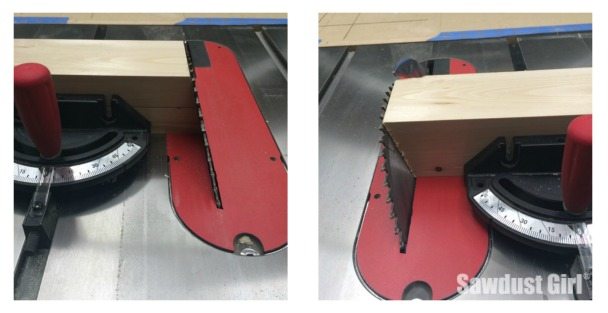
Step 2 – dry fit
- Before you start gluing, joining or fastening your table legs together, set all your parts together and make sure they fit, are the proper width and height.
- You definitely want to discover any brain fart mistakes (I have those all the time – don’t feel bad) BEFORE you start glueing up!
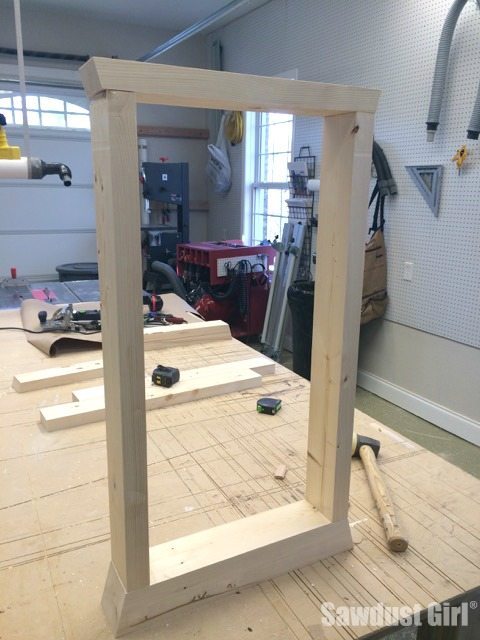
Step 3 – Assemble Legs
- Decide what type of joinery you will be using.
- Pocket hole screws are an easy option if you have a pocket hole jig. (check out my reviews if you are considering purchasing one)
- If you use a pocket hole jig, make sure you use plugs before you finish you piece. Your piece will more professional if there are no visible pocket holes.
- Dowels are are an easy method and don’t require more than a simple dowel centering pin, proper drill bit and wood dowel. You can get a Dowel Kit for about $5.
- I’m using mortise and tenon joinery. I have a Festool Domino, a pricey but amazingly easy to use and accurate tool.
Whatever your method, use wood glue and assemble those legs.
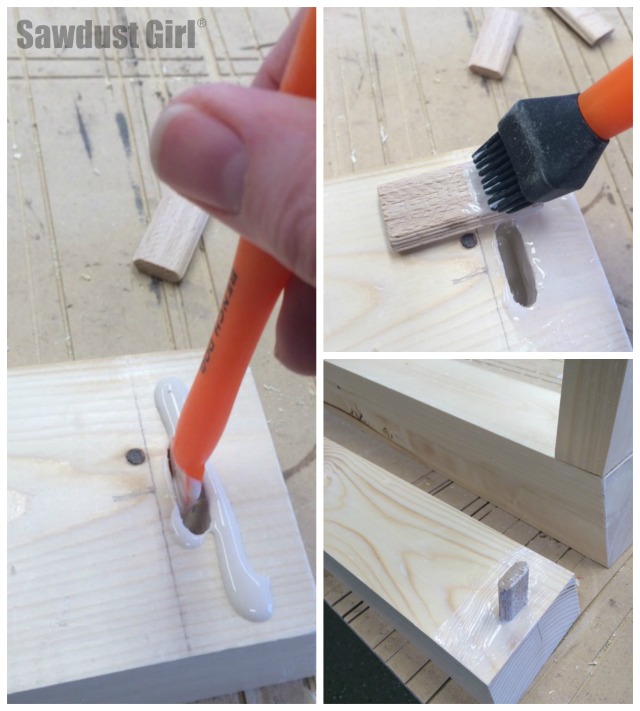
Use assembly squares or corner clamps to make sure your legs are square during assembly.
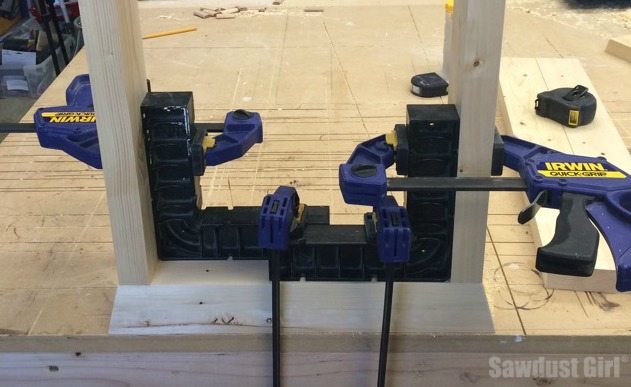
Use clamps to hold everything in place while the glue sets up.
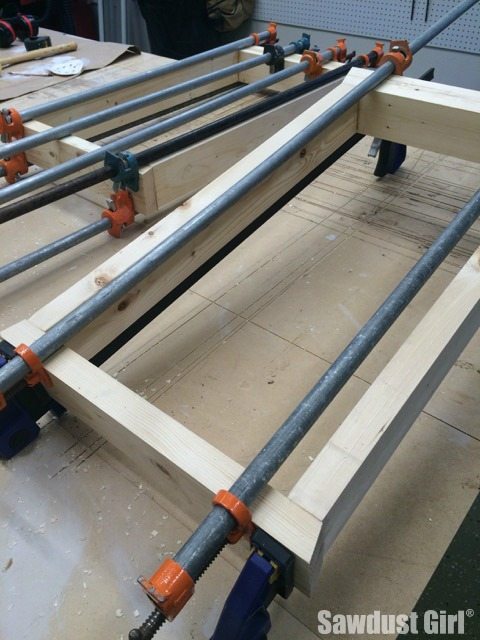
Optional Step
- I added small pieces of wood to the bottom of my legs. Just for added visual interest.
- Cut four pieces of 1×4 pine 4″ wide
- Cut each side of these on a 15˚ angle
- Glue and clamp these to the bottom of your legs
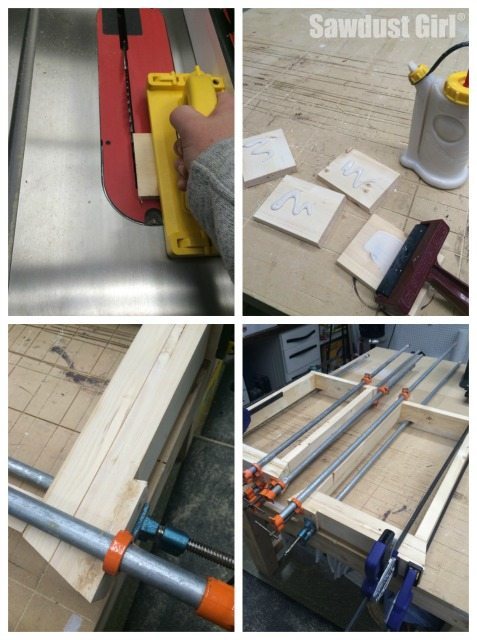
Step 4 – Sand and finish legs
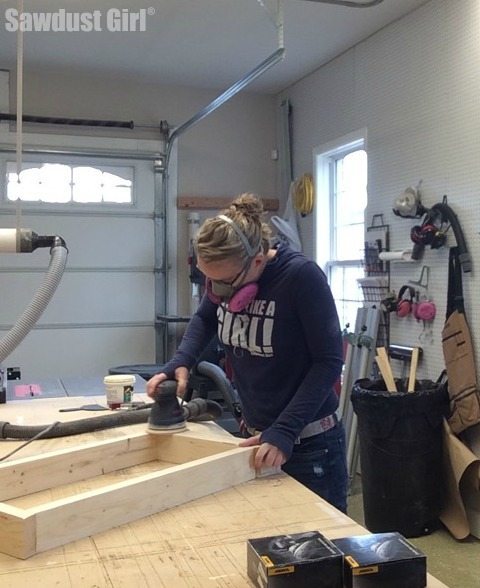
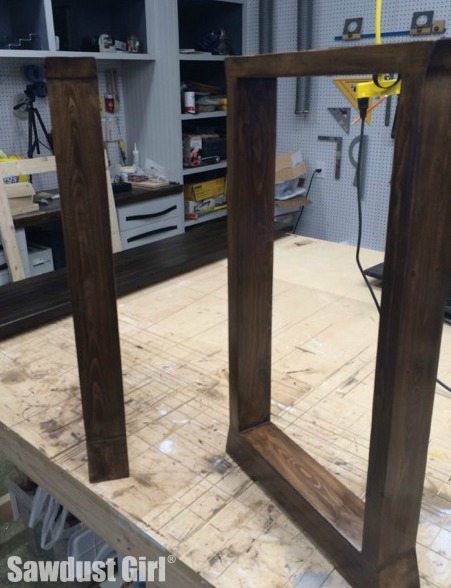
Create bottom shelf
- Join wood together using glue and clamps
- OR trim some reclaimed lumber down to size to create your 12″ wide lower shelf.
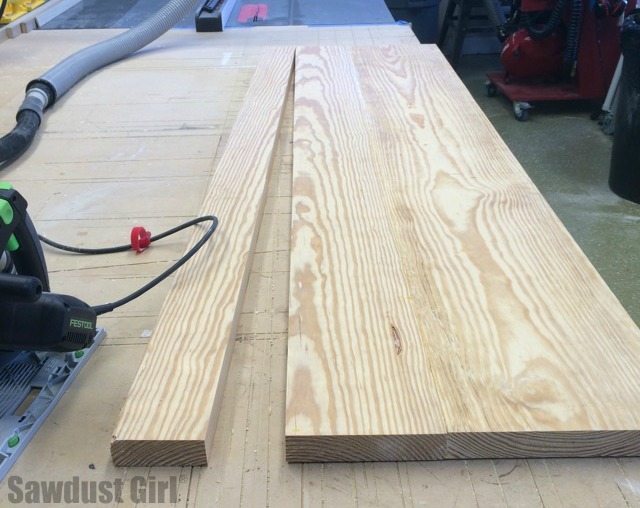
Attach lower shelf to legs
The length of the shelf can be adjusted to meet your needs.
- Dowels or loose tenons would be a great option here.
- See this post on working with Dowels
- Or screw up through the bottom of the leg parts into the bottom shelf with wood screws.
- Make sure your screws are not too long. Don’t want the screw coming up through the otp.
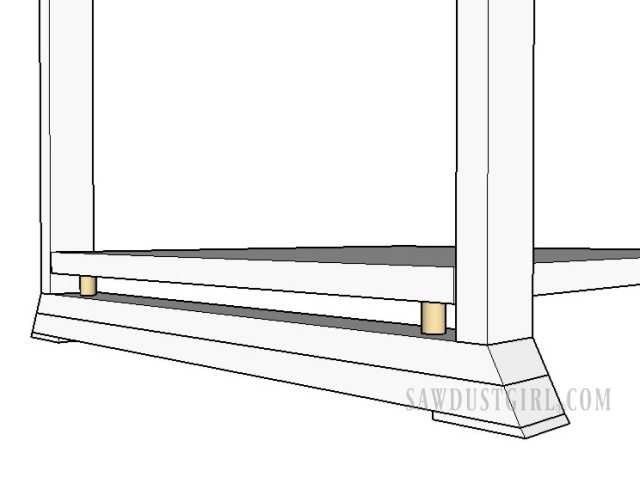
Create X’s
The X will be added on top of the lower shelf so you need to make sure the lower shelf is in place before you measure and cut you X’s.
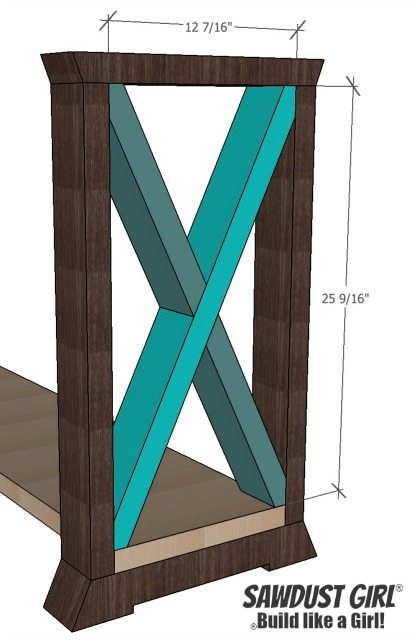
The exact height and width of your table legs will effect the angles on your X pieces. To get angles that will fit your console table perfectly, it’s best to measure and get the perfect angles for the space you end up with. The ends of your X pieces will look something like this.
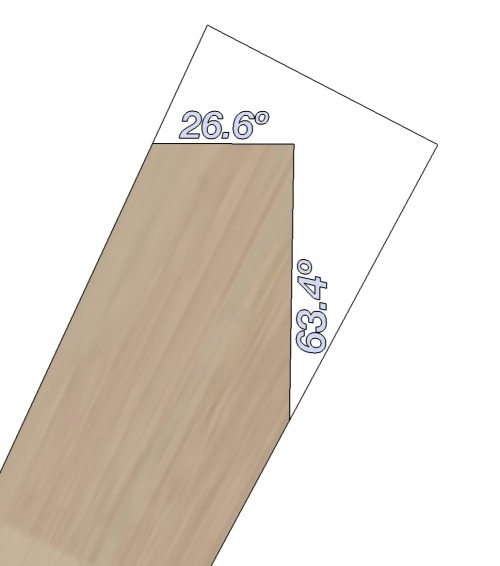
The best way to fit your X to your table leg is to hold each piece in place and mark where it intersects with the table leg.
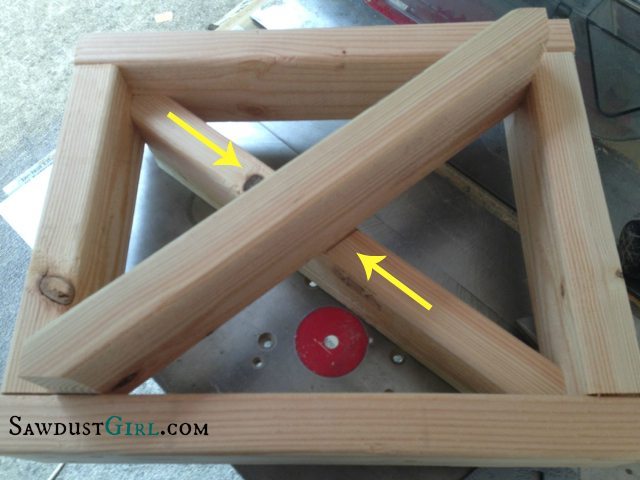
Where the boards in the X intersect, mark them but only cut halfway through. (I show you how to do that in this post)Then you can slide them together and you have an X with out any visible fasteners.
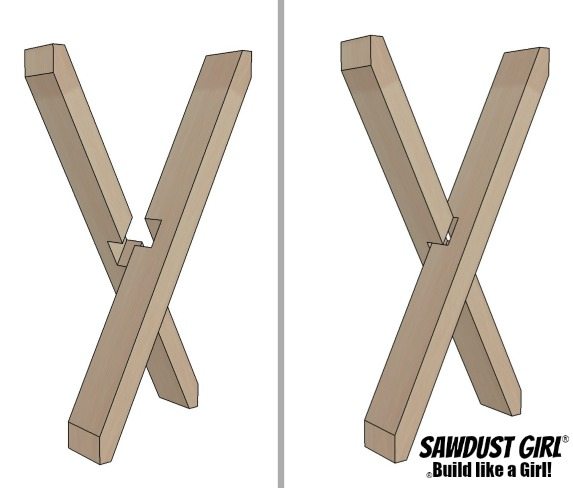
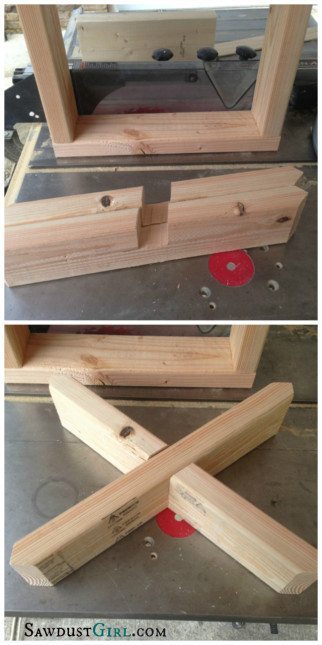
Dry fit then finish X’s
- Dryfit your X’s to make sure they fit.
- Paint, stain or clear coat your X’s. It will be easier to do this before you attach.
Attach X’s to your box leg console table legs
- Since you haven’t attached the top yet, you can drive screws directly down from the top into the boards that form the X.
- To hold the bottom of the X boards in place, use brad nails so you don’t have much of a hole to patch.
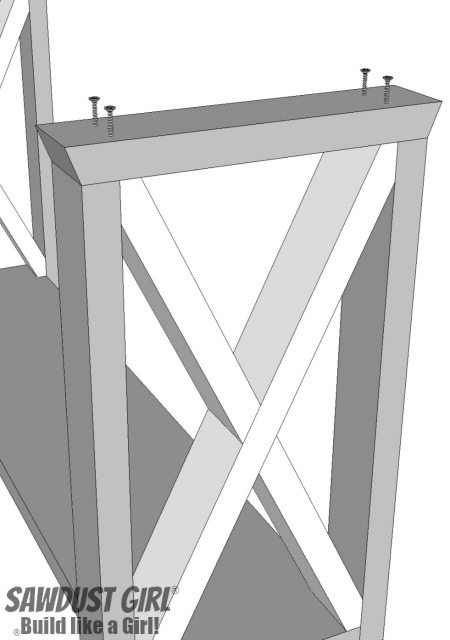
Step 5 – Build Finish and Attach table-top.
- Join several pieces of 2x lumber to achieve desired width (or greater than desired and then cut down to size) for table top and lower shelf. (Countertop Tutorial)
- Attach the top to the legs. A small block of wood attached to the top inside of each leg will give you a good access point to attach the table top. Make sure you allow for wood movement of the top slab.
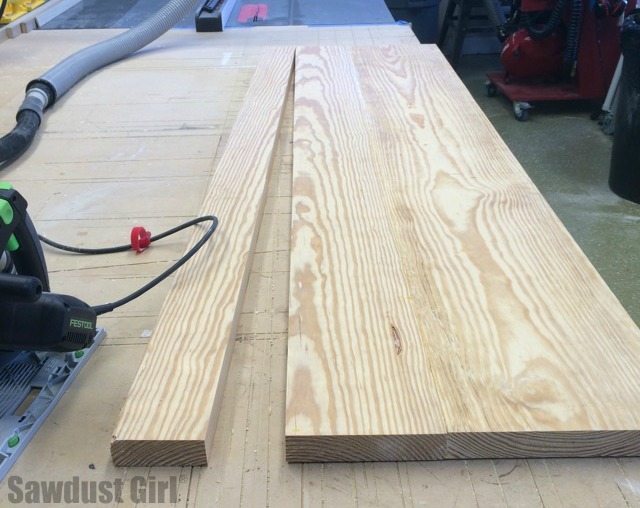
Sand and finish your box leg console table to your hearts content. This is a concoction of a bunch of stain colors darkened with ZAR Black Onyx and then 3 coats of tung oil.
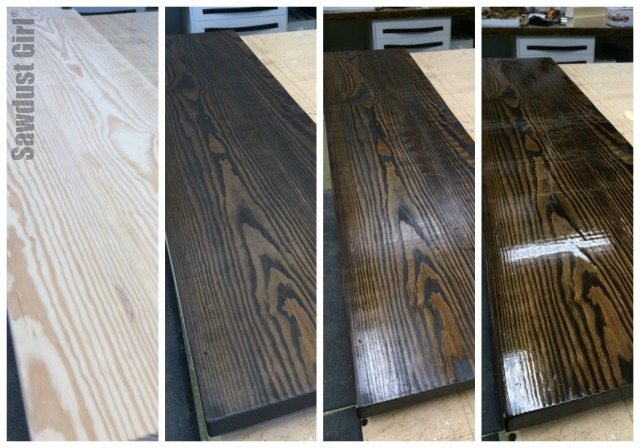
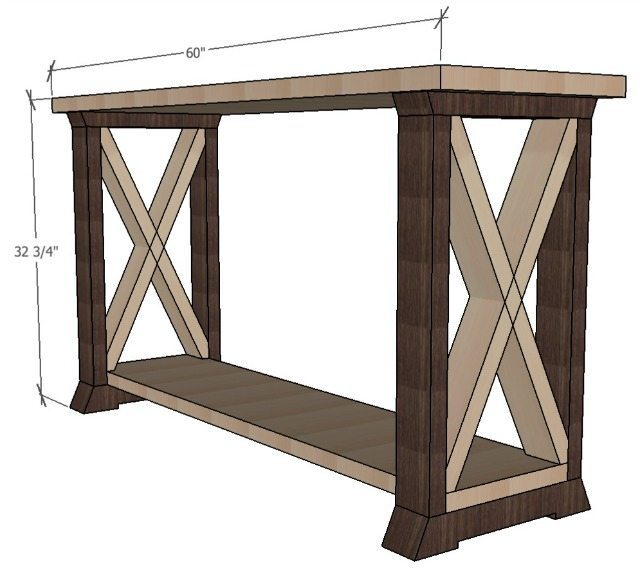
Enjoy your BoX Leg Console Table!
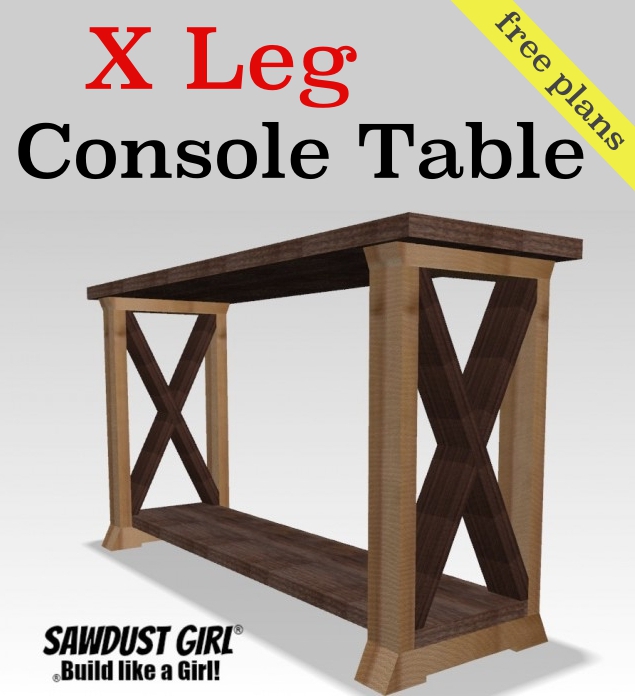
Sorry I don’t.
Do you have a start to finish .pdf for this project? I like to print and take out to my garage when I build something rather than the computer. And all of the ads are in the way!
Thanks!
Adding the X’s is completely optional so leaving those out will make this an easier first project table! You’ll have to make adjustments to the sizing of the parts to create the table size that you want. Figuring out how to plan a project is really important part of building. Modifying existing plans is a good way to start.
How do I make a 5 ft long by 19 in wide by 33 in tall without the X in the legs and I want just straight legs. Also what size on the bottom shelf? As you can probably tell this is my FIRST DIY table.